Keeping the vessels in shape: the challenges of dry docking a vessel.
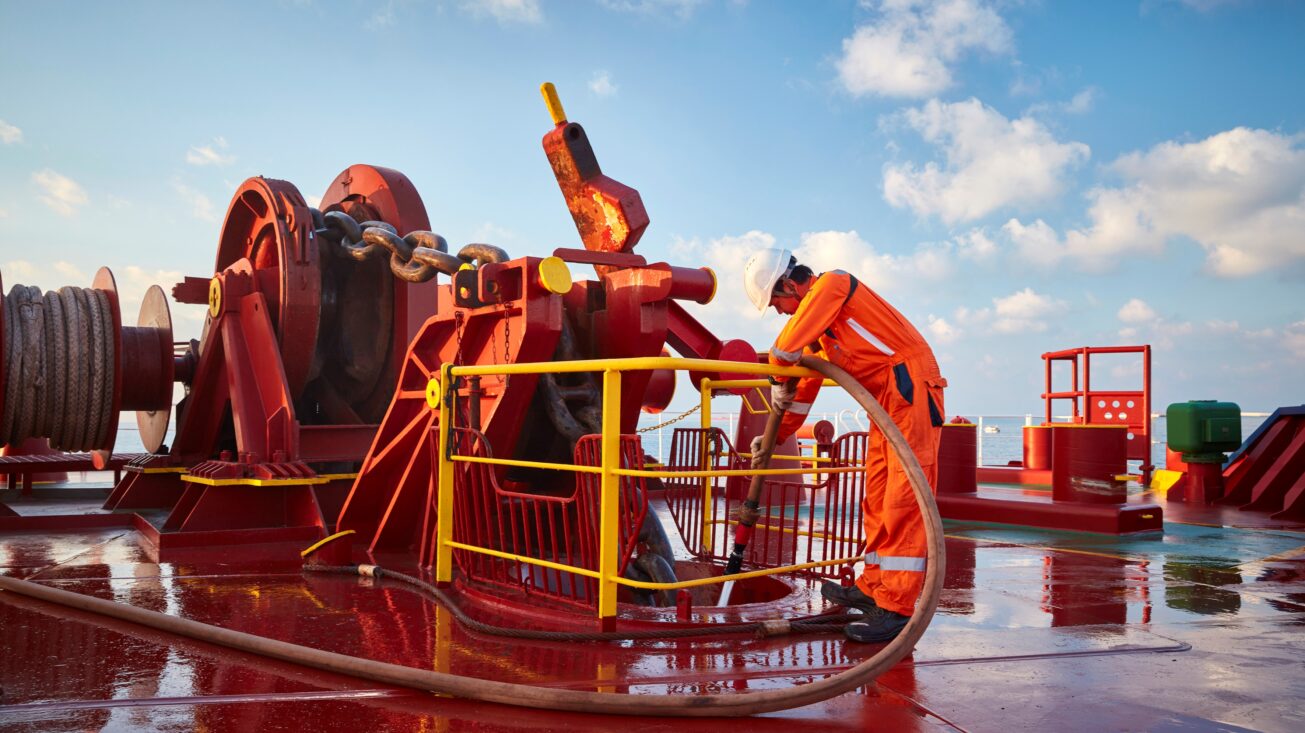
From the very day a vessel is delivered, ship managers have a binding obligation to keep it in shape.
According to the IMO MARPOL and Safety of Life At Sea (SOLAS) convention, the most important of all international treaties concerning the safety of merchant ships, vessels require a complete inspection of their underwater hull twice within a five year period, apart from the Class and Statutory Annual Hull and Machinery Surveys. One of these hull inspections is performed no later than 3 years from the day a vessel is launched, or from the previous dry docking project; for vessels less than 15 years old, an in ‘Water Survey in Lieu of Docking’ usually takes place. The second hull inspection is done via a dry docking survey within the ‘Special Survey’ time frame, which is undertaken every five years, and commences 15 months prior to the expiration date of the vessel’s statutory trading certificates. The dry docking survey is part of the more extensive dry docking and repair project, whereby the vessel enters a ‘floating’ or ‘graving’ dock in the shipyard so all parts which are normally under water can be more thoroughly examined, including not only the hull but also the propeller, rudder and sea chests.
The dry docking project is one of the most challenging assignments a Technical Superintendent Engineer is responsible for; making sure the vessel is maintained so that it can fulfill its commercial missions safely and efficiently. Quoting Elias Kontaxis, Fleet Manager at Thenamaris who has attended as Superintendent Engineer and supervised as Fleet Manager over 55 dry docking projects during his career thus far, “The dry docking is the most demanding challenge during the vessel’s five-year cycle. It certainly is a regulatory commitment, but more importantly it is the opportunity we have to address the wear a vessel accumulates while it is in operation, and to get it back in shape.”
The ideal timing of the dry docking project should be decided upon with the mutual agreement of the commercial team responsible for chartering the vessel and the technical team responsible for maintaining it. “In determining the most appropriate time to schedule the dry docking, it is important to bear in mind that we would not want to miss a particularly attractive period in the spot chartering market because the ship is in dry dock. However, on the other hand, we must meet our maintenance and upgrading obligations within the required timeframe,” remarks Elias.
The need for communication and coordination in a dry docking project extends to its execution. The dry docking is an orchestrated effort involving multiple stakeholders including not only the ship manager but also the vessel’s classification society, its flag state, the shipyard, repair teams, various subcontractors, specialists and consultants. All of these parties must work together to ensure the vessel’s condition meets regulatory requirements, including retrofit requirements. During dry dockings, work that will enhance the vessel’s commercial attractiveness and performance may also be undertaken.
A dry docking project may last from ten days to several weeks, depending upon the maintenance and upgrades to be performed. For example, ballast water tank treatment works are very time consuming and can significantly prolong the duration of the survey. Managing the time and costs associated with a dry docking project is one of the other challenges, as both of these factors must be considered in relation to the final quality of the end result.
“You have to prepare everything very well in advance, starting with a solid specification of the works to be done. You also have to be ready to proceed with the dry docking earlier than Class Rules due dates when freight levels are lower such that the opportunity cost of not being available for hire is less,” says Elias. He adds, “And as you go along it is important not to forget that communication and common sense are the most powerful weapons you can use to solve events you had not anticipated.”
The Superintendent Engineer has overall responsibility for the works, from start to finish. He has to issue the dry docking specification and prepare the budget, coordinate orders for stores and spares, select the shipyard, subcontractors and specialists, communicate with the Classification Society and other parties, as well as liaise with the Insurance Underwriters and Club Inspectors in case of Insurance or General Average Claims. Upon completion of the project, he must then attend the sea trials, submit the final works reports and approve the invoices.
The Superintendent Engineer cooperates closely with the relevant Marine Superintendent who is primarily dealing with safety-related issues on the vessel ensuring that the dry docking project itself occurs in a safe environment. “Just imagine 50 people of various nationalities working at the same time in different areas of the vessel…you have to make sure that safety procedures are being followed and that no individual is in danger,” says Captain Gerasimos Soulanis, Marine Superintendent in Thenamaris’ Safety & Quality Department who has also been involved with a large number of dry docking surveys throughout his career. He explains, “Such efforts are very challenging, but the end result is also very rewarding.”